Not really news, but today I’ve been working on two MS model necks.
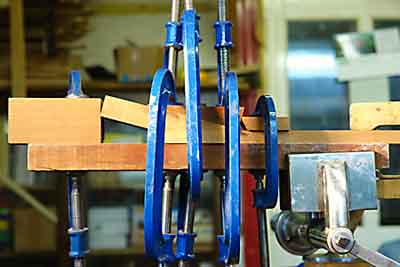
I join the head to the neck with a scarfe joint, the strongest and simplest I know.
Here is the head glued and clamped to the neck. Because the pressure is at an angle to the joint and glue acts as a lubricant when first applied, I clamp pieces of wood at either end to stop the head sliding from its correct position.
Not a good photo – the spring clamps hold the head veneer in place while the glue dries. A plywood pad spreads the load and prevents damage to the veneer. The head will be taken to correct thickness after the tuner holes are drilled.
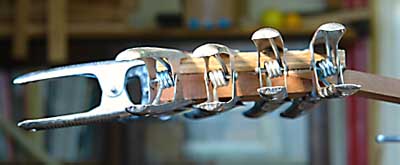
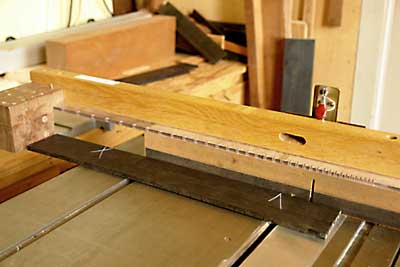
The neck cannot be taken to its final shape without its fingerboard; here the fingerboard is being slotted by being passed over a fine saw blade by a fret-slotting jig. The slots in the jig control the distance the fingerboard is moved each time for the next slot. This distance is detirmined by a pin which fits into slots on the jig. These are not the slots you can see, but another set on the far side of the jig.
After slotting it, I’ll cut the fingerboard to size.
Here is one neck shaped to its fingerboard (and with the head also shaped) and another about to be shaped. This is done by running fingerboard and head template past a router bearing so that the cutter cuts the wood to the same shapes.
The fingerboards are taped on temporarily and will now be removed. They will be glued on permanently after the necks are fixed to the bodies.
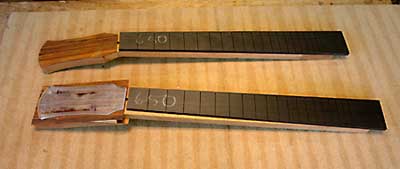
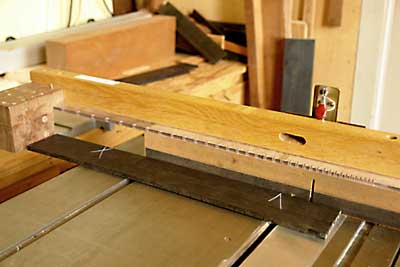
Tomorrow I plan to finish these necks and fit the heel-blocks. Then I shall bind the MS model I have ready and then be able to join neck and body. Then I can glue the fingerboard in place, shape the neck and fit the frets.