Wood and materials
Timber
The timber used in building instruments has a big influence on how they sound; good design in itself is not enough. The best wood has a ring to it; not for nothing are instrument building woods known as tonewoods. Whether hardwood or softwood, if it doesn’t have a good tap tone it is unlikely to make a great instrument.
I take a great deal of trouble finding and buying the best wood available; in relation to the small number of instruments I build I have good stocks. This means my wood is stacked and seasoned for years before being used; thoroughly seasoned air-dried wood makes the best sounding and most stable instruments.
If I had to find twice as much wood as I use now, I’d have trouble maintaining the same quality; if I had to find ten times as much or more, I know I couldn’t. A luthier building one or two instruments a month can select outstanding wood in a way that a shop building fifty a month must struggle to do; factories building hundreds a month or more must have a very hard time.
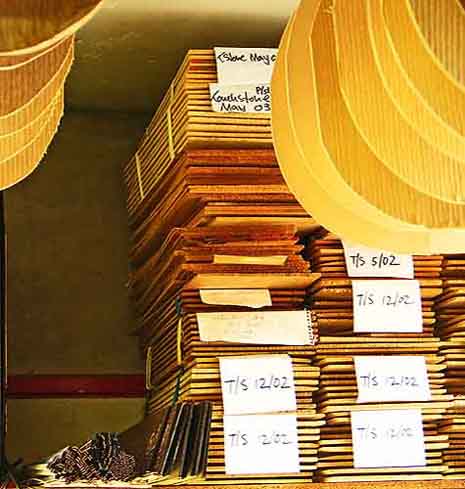
Soundboards
I build many of my instruments with soundboards of German spruce. This gives a combination of power and subtlety that is hard to match. It takes a couple of years to approach its full potential, opening out into warmth and power without losing its clarity and ring and sustain.
Every few years I visit suppliers in Germany and select what I consider to be the very best. This is stacked and stored for years before use. I also buy from UK dealers, sorting through their stock and selecting only the very best wood.
I also use Adirondack (American Red) spruce and Italian spruce. Adirondack was used as soundboard material on classic US guitars of the 1920s and 1930s; I use it primarily on my New World model guitars but it also makes an interesting alternative to European spruce on other flat-top instruments. Like Adirondack, Italian spruce is a Red spruce. It has a combination of the warmth of German spruce and the response of Adirondack.
I now also build soundboards with figured (bearclaw) Sitka spruce. After trying Sitka many years ago and not liking the instruments built with it, I have recently realised there is Sitka and there is Sitka. The best Sitka can make great sounding instruments.
Backs and sides
On citterns, bouzoukis and guitars, I make backs and sides from a variety of rosewoods.
Best old Brazilian rosewood is rightly regarded as making wonderful guitars. My stock is cut from logs cut between 30 and 50 years ago and includes the best quality very dark brown Brazilian. This can be very regular and even, or more decorative with vivid pink or orange stripes.
I also have a stock of reclaimed Brazilian rosewood, some of which is not only a great tonewood, but is also colourful and decorative. Like all my wood, this is absolutely ethical and legal with full authentic CITES documentation.
As well as these sets, I have a quantity of scantlings (see top picture), small section lengths of top quality wood which are cut and joined to make multi-piece backs and sides (see news item 14 August 2005). This is a time consuming business, but it’s a pleasure to work with such wonderful wood.
Brazilian rosewood guitars have exceptional clarity and projection. It’s easy to understand why it has been so highly regarded over the years.
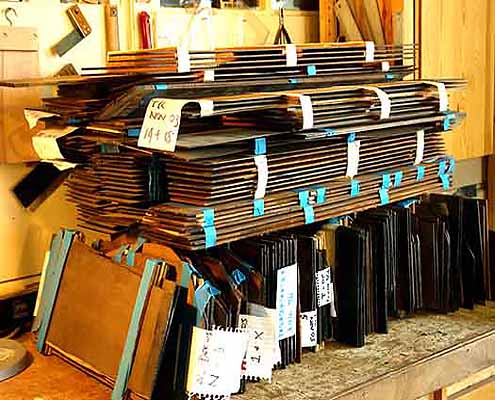
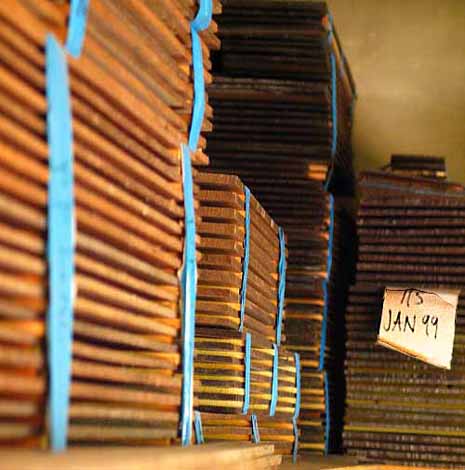
Good Indian rosewood is similar to Brazilian, but gentler sounding. It’s been the standard instrument building rosewood for over forty years. Mine is a minimum of nine years old, air-dried in my shop.
With restrictions on the use and shipping of Brazilian rosewood, luthiers everywhere are investigating alternatives. I have a good stock of African Blackwood, which gives instruments a deep, solid tone.
Wengé is not easy either to work or to lacquer, but can be a good alternative to mahogany for necks.
I’m now also building with Malaysian Blackwood which I’m using for backs and sides on guitars and citterns. Its appearance varies considerably, the sets I use are a subtle dark colour. Although not related to African Blackwood, it gives instruments a similar sound.
Maple makes wonderful (carved back) mandolins and mandolas. I use birdseye maple from Canada and northern US; very pretty, it’s harder than European maple and gives a clear smooth sound.
Necks
The wood used to make a neck does more than keep it straight. As with all materials used to build a guitar, it has an effect on the sound of the instrument and must be well matched with the body.
For many years I used Mahogany for all necks but now also use Wengé. This has a similar ring and stiffness to Brazilian rosewood (which I have used for necks occasionally in the past) but is lighter in weight. Because of its stiffness, a Wengé neck can be slimmed down without losing rigidity.
Fingerboards and bridges
Fingerboards and bridges are all made from seasoned ebony. Ebony fingerboards are stiff and hard-wearing and feel good under the fingers.
I’ve built guitars with rosewood bridges in the past but prefer the clear solid sound from an ebony bridge.
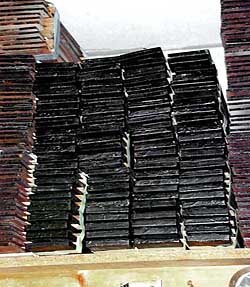

Lacquer
All instruments are lacquered by David Wilson with 2007 compliant melamine lacquer. This is applied in a series of thin coats each of which is allowed to dry for several days before being rubbed down. After another week or so to dry and harden it is flatted and buffed to a high gloss. The complete process takes around a month.
David has been lacquering my instruments for the last 25 years or so and is simply the best.